Electric Vehicle battery market globally is projected to grow at a CAGR of 25.3%, expected market growth in USD 27.3 billion in 2021 to USD 67.2 billion by 2025. Because of Government policies and regulations there is a huge demand of electric vehicles which highly progresses improvement in battery technology. All big companies planning to launch of new plug-in EV models in coming 2-3 years, which will create base for EV market in all Countries. Because of high environmental impact norms and Global policies for Environmental pollution today, all Governments around world are encouraging the adaption of vehicle with minimum or zero emission.
It is recommended now for any OEM or EV startup to perform analysis and validation on battery cell or pack to check performance of different cooling methods. Computational Fluid Dynamics Software and Structural Software must be used to replicate flow distribution around the cells and the pack and also to check strength of battery casing. Validation through software creates more robust design and it can be virtually tested for all possible conditions. In validation maximum temperature in battery pack, coolant and temperature difference is compared with each other.
Liquid cooled and Air cooled process can be designed, validated and optimized using CFD and CAD tools. Also Structural durability, crash, drop and Handling CAE tests will validate the design of casing and battery pack. Because of this approach life of battery and time to launch into market can be improved exponentially.
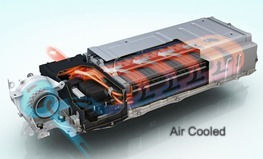


Observations and Results Achieved Using this approach:
Air cooled, indirect liquid cooled and direct liquid cooled thermal management solutions compared using computational fluid dynamics. CFD can be used intensively in order to generate best possible cooling technique for complete battery pack.
Actual Road load data used to perform dynamic behavior. Notch test and crash test using multiple software helped in designing the best model ready for prototype.
This approach saves time to market by 70% and Total cost of project reduced by 75%.

Comments